Why a Welding WPS is Crucial: Enhancing Consistency and Compliance
Why a Welding WPS is Crucial: Enhancing Consistency and Compliance
Blog Article
Unlocking the Power of Welding WPS: Techniques for Efficiency and Security in Fabrication
In the realm of fabrication, Welding Procedure Specs (WPS) stand as the foundation of welding operations, dictating the essential steps for achieving both efficiency and safety in the manufacture procedure. Comprehending the intricacies of WPS is vital to harnessing its full potential, yet several companies struggle to unlock real power that exists within these documents (welding WPS). By delving into the strategies that optimize welding WPS, a globe of boosted efficiency and heightened security awaits those happy to check out the nuances of this important facet of construction

Importance of Welding WPS
The significance of Welding Treatment Requirements (WPS) in the construction market can not be overemphasized. WPS function as an essential roadmap that outlines the needed actions to guarantee welds are performed consistently and appropriately. By specifying important criteria such as welding procedures, materials, joint designs, preheat temperatures, interpass temperature levels, filler metals, and post-weld warmth treatment requirements, WPS supply a standard strategy to welding that enhances effectiveness, top quality, and safety and security in construction procedures.
Adherence to WPS aids in attaining uniformity in weld top quality, lowering the possibility of issues or architectural failings. This standardization likewise assists in conformity with industry policies and codes, making certain that fabricated frameworks satisfy the called for safety standards. Additionally, WPS paperwork makes it possible for welders to replicate successful welding treatments, leading to constant results across various projects.
Fundamentally, the careful growth and rigorous adherence to Welding Treatment Specifications are extremely important for promoting the honesty of welded frameworks, safeguarding versus possible risks, and promoting the credibility of fabrication firms for providing high-quality services and products.
Crucial Element of Welding WPS
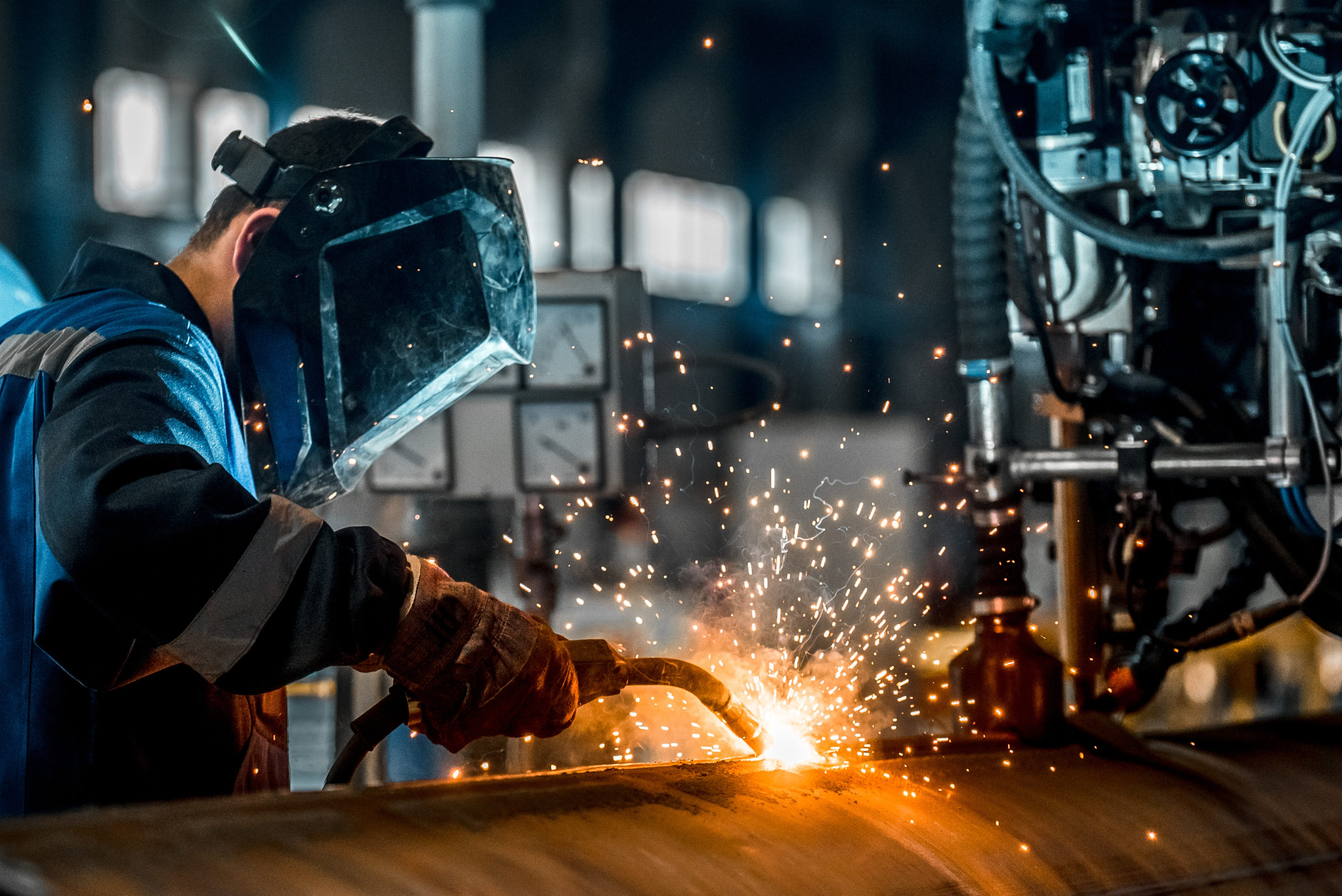
Enhancing Effectiveness With WPS
When enhancing welding procedures, leveraging the crucial aspects outlined in Welding Procedure Requirements (WPS) becomes important for optimizing and enhancing procedures performance. One method to improve effectiveness with WPS is by meticulously picking the ideal welding criteria. By sticking to the certain standards supplied in the WPS, welders can make certain that the welding devices is established properly, bring about high-quality and constant welds. In addition, adhering to the pre-approved welding series index detailed in the WPS can substantially reduce the time invested in each weld, inevitably enhancing general performance.
Frequently reviewing and upgrading the WPS to incorporate any lessons found out or technological improvements can likewise add to efficiency improvements in welding operations. By welcoming the guidelines established forth in the WPS and continuously looking for methods to maximize procedures, fabricators can attain greater efficiency levels and remarkable end outcomes.
Ensuring Security in Manufacture
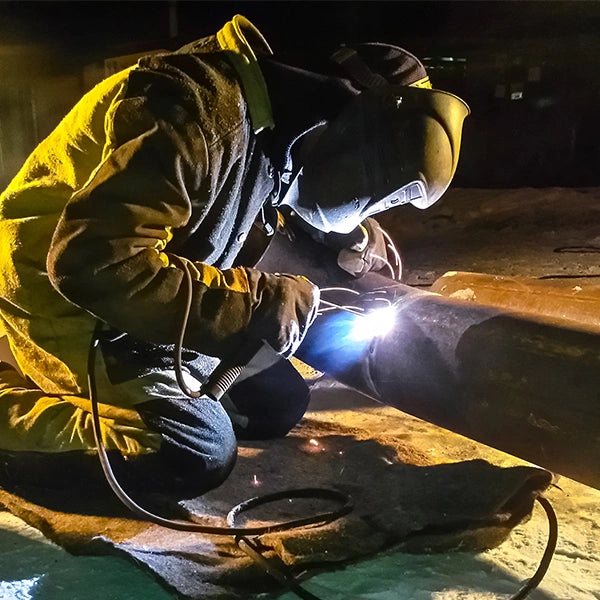
Security protocols in fabrication play an essential function in securing employees and optimizing functional procedures. Guaranteeing safety and security in fabrication entails a our website multifaceted method that includes numerous aspects of the welding process. One basic facet is the arrangement of personal safety equipment (PPE) tailored to the specific risks existing in the fabrication environment. Welders have to be equipped with proper gear such as headgears, gloves, and safety clothes to reduce risks connected with welding activities.
Moreover, adherence to proper air flow and fume removal systems is crucial in preserving a healthy and balanced work environment. Welding fumes contain hazardous compounds that, if breathed in, can posture major wellness risks. Applying reliable air flow procedures assists to decrease direct exposure to these unsafe fumes, promoting breathing health among employees.
Regular equipment upkeep and assessments are additionally essential for ensuring security in manufacture. Defective machinery can result in injuries and mishaps, highlighting the relevance of routine checks and timely fixings. By prioritizing precaution and fostering a society of understanding, manufacture facilities can develop a effective and secure workplace for their workers.
Executing WPS Finest Practices
To boost functional performance and guarantee quality results in manufacture processes, incorporating Welding Procedure Spec (WPS) finest techniques is critical. Choosing the appropriate welding procedure, filler material, and preheat temperature level specified in the WPS is crucial for achieving the preferred weld high quality. Ensuring that certified welders with the necessary qualifications lug out the welding procedures according to the WPS guidelines is important for consistency and reliability.
Verdict
In verdict, welding WPS plays an essential duty in making sure efficiency and security in fabrication processes. By complying with these methods, organizations can unlock the full potential of welding WPS in their fabrication procedures.
In the realm of fabrication, Welding Treatment Specs (WPS) stand as the backbone of welding procedures, determining the required steps for attaining both effectiveness and security in the fabrication process. By specifying vital specifications such as welding processes, products, joint designs, preheat temperatures, interpass temperatures, filler metals, and post-weld warmth therapy demands, WPS offer a standardized method to welding that improves performance, high quality, and security in manufacture processes.
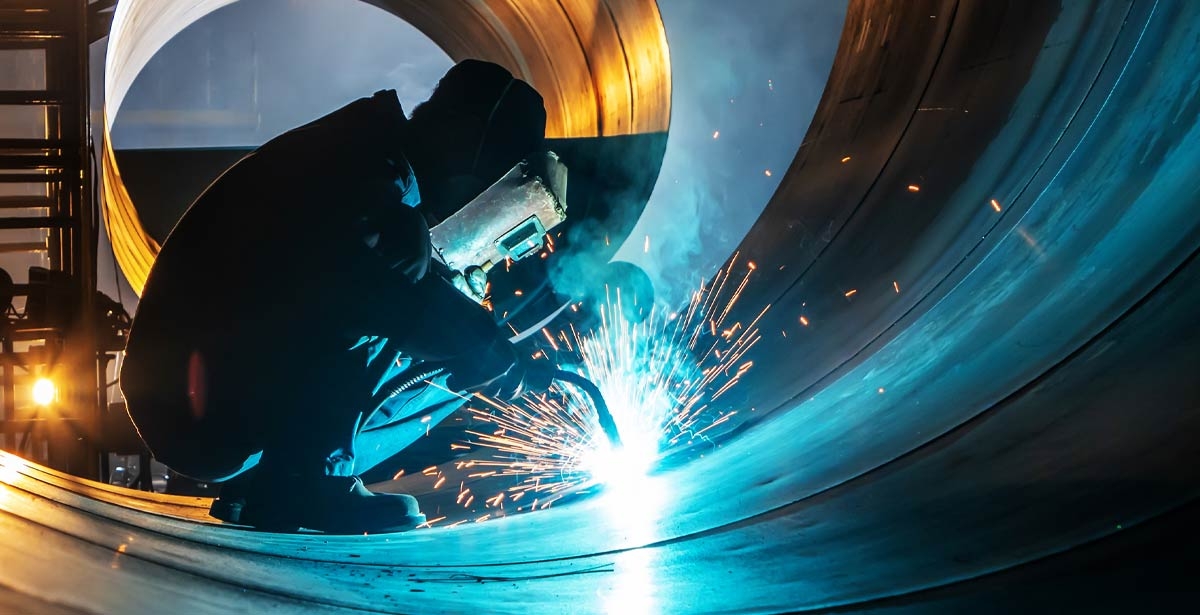
When optimizing welding procedures, leveraging the vital elements detailed in Welding Treatment Requirements (WPS) becomes vital for streamlining processes and optimizing efficiency. (welding WPS)
Report this page